Orange County Fleet Services Blog
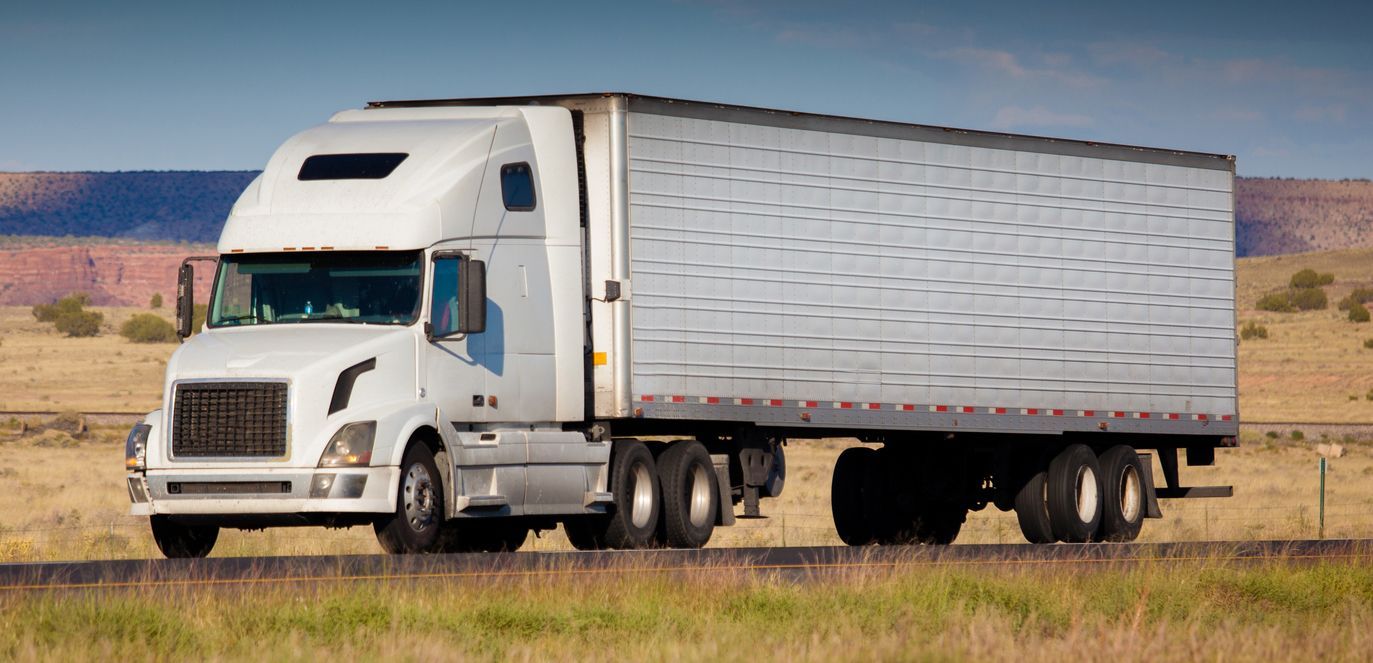
Tire blowouts are a major safety concern for semi truck drivers and other motorists on the road. When a blowout occurs, it can lead to loss of control, accidents, and costly downtime. Given the size and weight of commercial trucks, tire failure can have especially serious consequences. Fortunately, many blowouts are preventable with proper maintenance and attention to driving conditions. But if your big rig does suffer a tire blowout, our team at Orange County Fleet Service can provide roadside help. Here are four common reasons why semi truck tires blow out. Underinflation Driving with underinflated tires is one of the leading causes of blowouts. When a tire doesn’t have enough air pressure, more of its surface comes into contact with the road, causing excess friction and heat. Over time, this heat can weaken the tire’s internal structure and lead to a sudden failure. Regularly checking and maintaining proper tire pressure according to the manufacturer’s specifications helps ensure safe operation and reduces the risk of blowouts. Overloading Carrying loads that exceed a truck’s rated capacity puts extra stress on the tires. The added weight increases pressure and heat buildup, which can cause the tire’s sidewalls to fail. Even a properly inflated tire can fail under the strain of an excessive load. It's crucial to follow weight limits and properly distribute cargo to prevent overloading any one axle or tire. Road Hazards Sharp debris, potholes, and rough road surfaces can all contribute to tire damage that leads to blowouts. A tire might not burst immediately after hitting a hazard, but the damage can weaken it to the point where it fails later on. Drivers should remain vigilant and avoid debris whenever possible, and tires should be inspected after traveling through particularly rough areas. Early detection of cuts or bulges can help prevent a more serious issue. Worn-Out Tires As tires age, the rubber compounds degrade, and the risk of blowout increases—especially under heavy loads or high speeds. Regular inspections and replacing tires when tread is low or sidewalls are damaged can help avoid dangerous failures. 24/7 Roadside Semi Truck Tire Services in Orange County, CA When you need semi truck tire services in Anaheim, CA and the surrounding area, contact Orange County Fleet Service at (949) 899-6802 . With our mobile service, we can come to you to address your semi truck tire needs!
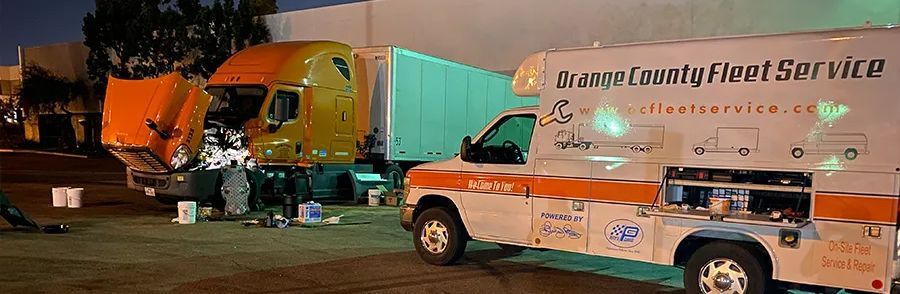
Roadside emergencies are never convenient, especially when you're behind the wheel of a semi truck. Whether it’s a flat tire, engine trouble, or brake failure, knowing how to respond quickly and safely can help protect you, your cargo, and everyone else on the road. When you need 24/7 roadside assistance in Anaheim, CA, or the surrounding areas, give Orange County Fleet Services a call. Pull Over Safely and Quickly At the first sign of trouble, signal and move to the shoulder or a safe area as soon as possible. Choose a spot with enough room for your truck and trailer, ideally away from curves or blind spots where visibility is limited. Secure the Area Once you’re stopped, turn on your hazard lights immediately. Place reflective triangles or flares at appropriate distances, typically 10, 100, and 200 feet behind the trailer on the traffic-facing side to alert oncoming drivers. Wear a reflective vest if you exit the vehicle, especially at night or in low visibility. Assess the Problem Perform a quick walk-around inspection if it’s safe to do so. Check for visible issues like a blown tire, leaking fluids, or a disconnected trailer line. If you suspect a mechanical issue beyond your ability to fix on the spot, avoid trying to drive further; you could cause more damage or risk an accident. Call for Professional Help Have a list of reliable roadside assistance services that specialize in commercial trucks. Be ready to provide your location using GPS or mile markers, your truck’s details, and a description of the problem. Many fleets also offer in-house emergency dispatch, so check your company’s protocols if applicable. Stay Calm and Stay Put Unless the situation poses immediate danger, such as a fire, it's usually safest to remain in your truck until help arrives. Keep communication devices charged and stay in touch with dispatch or authorities if needed. 24/7 Roadside Assistance in Orange County FSI powers Orange County Fleet Services’ mobile response team in collaboration with Richard Petty Garages. This allows our certified roadside repair technicians to provide fast and accurate services around the clock for all types of vehicles, including big rigs, RVs, motorhomes, trailers, rental cars, buses, work trucks, delivery vans, construction equipment, and other fleet vehicles, big and small. Whether you’ve suffered a commercial vehicle breakdown and need to get back on the road fast, require roadside brake repair, or are looking for on-site maintenance for heavy equipment, we’ve got you covered. Give us a call at (949) 899-6802 to request an estimate or dispatch for immediate 24/7 mobile fleet repair in OC.

A fully loaded big rig relies on a responsive and reliable steering system to stay safe on the road; that’s why steering problems can be downright dangerous. Whether you're hauling cross-country or sticking to local routes, understanding common steering issues and how to fix or prevent them is key to keeping your truck running smoothly. When your semi truck needs steering repair in Anaheim, CA, or the surrounding areas, give Orange County Fleet Services a call. Loose or Wandering Steering If your truck feels like it’s drifting or the steering wheel doesn’t respond right away, it could be due to worn-out steering components like tie rods or the steering gearbox. This can make it harder to keep the vehicle centered, especially at highway speeds. To fix it, mechanics will typically inspect the entire steering linkage and replace worn parts. Regular maintenance checks can help catch these issues before they become serious. Power Steering Fluid Leaks Low or leaking power steering fluid is a common problem in commercial trucks. If turning the wheel feels stiff or you hear whining noises while steering, fluid levels might be the culprit. This issue often stems from cracked hoses or worn seals. Topping off the fluid is a temporary fix, but the real solution is repairing the leak at its source. Uneven Tire Wear and Alignment Problems If the truck pulls to one side or the steering wheel vibrates, alignment or suspension issues may be to blame. Poor alignment puts extra strain on the steering system and can cause tires to wear unevenly. A proper wheel alignment, regular tire rotations, and checking for bent or damaged suspension components can solve and prevent this problem. Steering Pump Failure The power steering pump is essential for smooth operation. If it fails, steering becomes heavy and sluggish. Replacing the pump and ensuring clean, fresh fluid is essential to keeping your steering responsive. Semi Truck Repair in Orange County At Orange County Fleet Services, our truck mechanics service all types of pickups, box vans, semis, cement trucks, water trucks, material handling equipment, and other light, medium, and heavy-duty trucks. From routine truck oil changes, fluid services, and truck tune-ups to complex diesel truck engine repair, truck transmission services, truck steering repair, and truck brake jobs, we do it all, in our shop or on the road. At the first sign of trouble, or when it is time for truck maintenance in Orange County, be sure to call us at (949) 899-6802 or visit our local big rig shop.
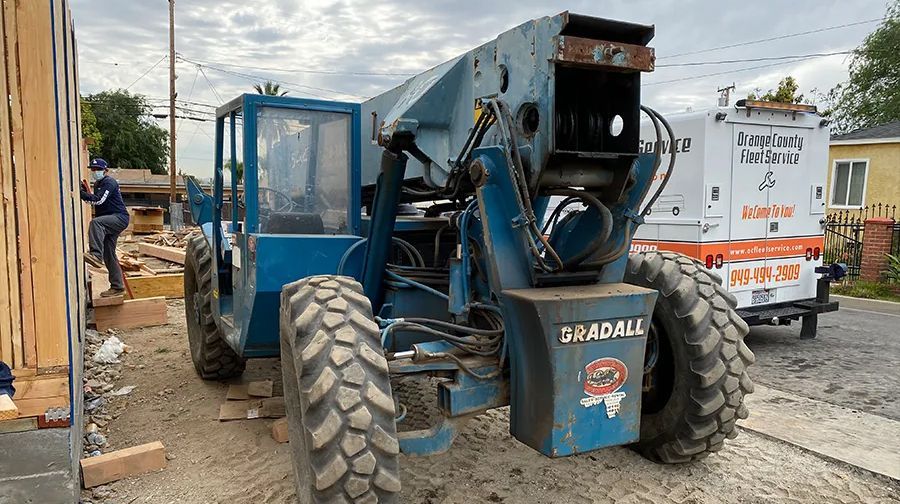
As the days get longer and Orange County starts heating up, it’s the perfect time to give your construction equipment a little TLC. Winter may be mild here, but even SoCal machinery needs seasonal attention. Whether you’re running excavators, loaders, or compactors, spring maintenance keeps your gear safe and ready to roll through the busy season. When you need construction equipment maintenance or repair in Anaheim, CA, or the surrounding areas, give Orange County Fleet Services a call. Inspect and Clean Everything Start with a full walkaround of each machine. Look for signs of wear, rust, or fluid leaks. Winter dust and grime can build up, especially if the equipment’s been sitting. Give everything a deep clean, paying special attention to undercarriages and air intakes. A clean machine doesn’t just look good, it runs better too. Check Fluids and Filters Engine oil, hydraulic fluid, coolant, and transmission fluid all deserve a close look. Top them off or change them according to your manufacturer’s schedule. While you’re at it, swap out dirty filters. Clogged air or fuel filters can reduce performance and cost you in the long run. Battery Health Matters Cooler months can drain battery life, so spring is prime time to test voltage and connections. Clean off corrosion and make sure terminals are tight. A weak battery can leave you stranded right when jobs start picking up. Tires and Tracks In Orange County, hot pavement and long workdays are coming fast. Make sure tires are properly inflated and show even tread wear. For tracked equipment, check for tension and any cracking or fraying that could cause downtime. Lubrication Is Key Grease all the necessary joints and pivot points to prevent premature wear. This simple task keeps your machines operating smoothly, especially during long hours on active job sites. Software and Tech Updates Many newer machines run diagnostics or have GPS and telematics systems. Make sure software is up to date, small updates can improve performance and even fuel efficiency. Construction Equipment Maintenance and Repair in Orange County Orange County Fleet Services performs all types of maintenance and repairs for just about anything with a motor. This includes backhoe repair, forklift repair, tractor repair, telehandler repair, skid-steer repair, excavator repair, and other construction equipment repair. Our team can provide fast service in our shop or in the field, all depending on your needs. From equipment engine repair and transmission service to hydraulic repair, track repair, and brake repair, we can restore the function of your heavy machinery. Give us a call at (949) 899-6802 to schedule an appointment or to request an estimate for the cost of construction equipment repair in Anaheim or a neighboring town.
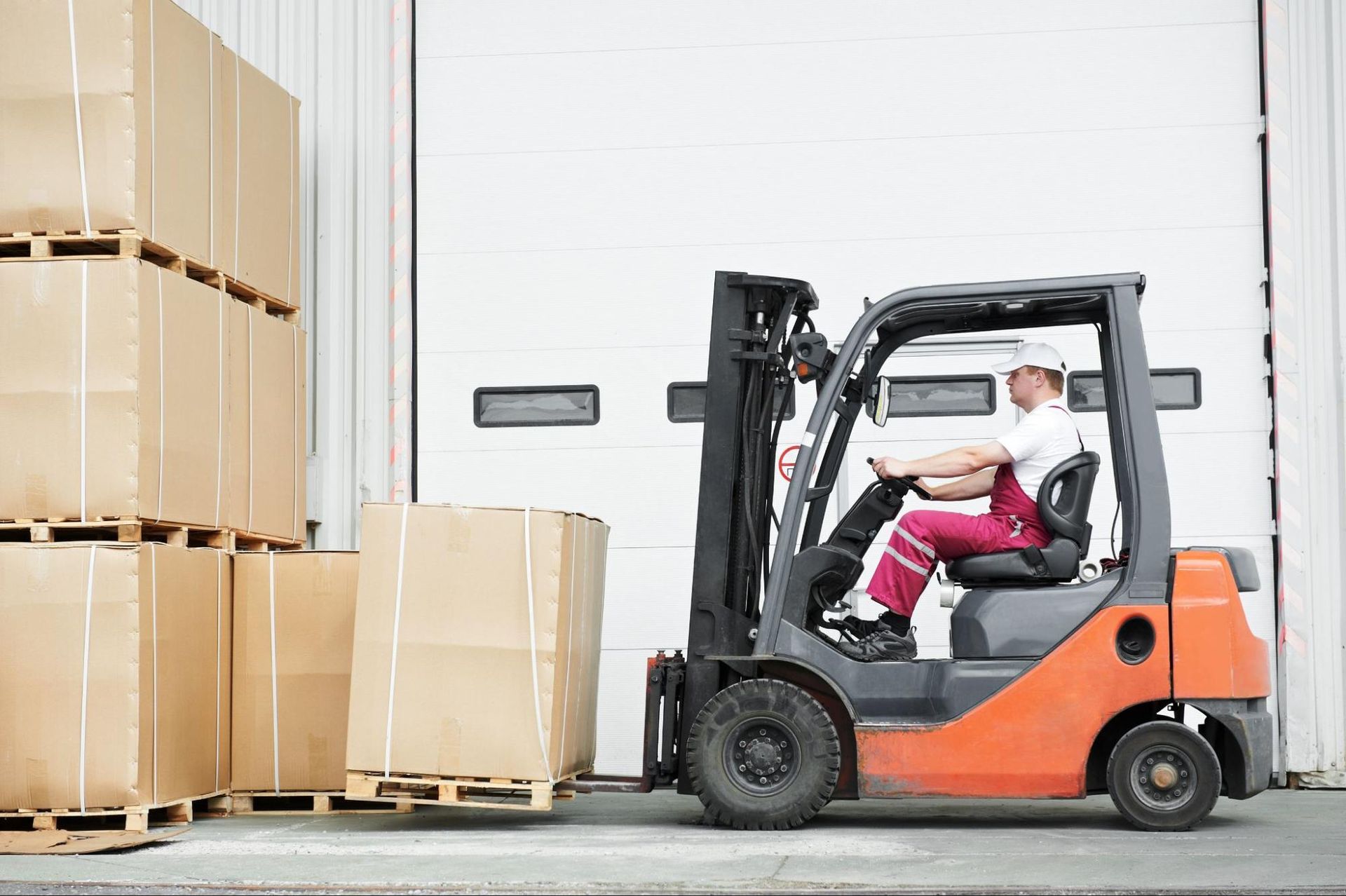
Forklifts are a staple of warehouses and industrial environments, but even the most robust machines can encounter issues over time. Understanding common forklift problems and their solutions can help you maintain peak performance and avoid costly downtime. When you need forklift or other construction equipment repair in Anaheim, CA, or the surrounding areas, give Orange County Fleet Services a call. Battery and Charging Issues One of the most frequent challenges with electric forklifts is battery-related problems. Over time, batteries can lose their capacity, leading to shorter run times and slower performance. Common solutions include regular battery maintenance—such as equalizing charges and cleaning terminals—to ensure optimal power delivery. If your battery is aging or not holding a charge, it might be time for a replacement. Keeping an eye on your battery’s performance and following the manufacturer’s charging recommendations can extend its lifespan and keep your forklift running efficiently. Hydraulic Leaks and Malfunctions Hydraulic systems are essential for the lifting and lowering functions of a forklift, but they’re also prone to leaks. A hydraulic leak reduces the efficiency of the system and can create slippery conditions and potential hazards on the shop floor. Regularly inspecting hoses, seals, and fluid levels can help catch leaks early. If a leak is detected, replace worn-out hoses or seals promptly. Additionally, scheduling periodic hydraulic system flushes and maintenance can keep everything operating smoothly. Tire Wear and Damage Forklift tires, whether cushion or pneumatic, are subjected to heavy loads and constant use, making them susceptible to wear and punctures. Worn or damaged tires can affect maneuverability and stability. Regularly checking tire pressure, tread depth, and overall condition can help you spot issues before they lead to accidents. Replacing tires when necessary and ensuring proper inflation are essential for safe operation. Brake and Steering Problems Brakes and steering systems are critical for operator safety. If you experience a spongy brake pedal, unusual noises, or difficulty turning, these could be signs of worn brake pads, low hydraulic fluid, or misaligned components. A thorough inspection by a qualified technician can diagnose these issues, and timely repairs can prevent accidents on the job. Construction Equipment Repair in Orange County Orange County Fleet Services performs all types of repairs for just about anything with a motor. This includes backhoe repair, forklift repair, tractor repair, telehandler repair, skid-steer repair, excavator repair, and other construction equipment repair. Our team can provide fast service in our shop or the field, depending on your needs. From equipment engine repair and transmission service to hydraulic repair, track repair, and brake repair, we can restore the function of your heavy machinery. Give us a call at (949) 899-6802 to schedule an appointment or to request an estimate for the cost of construction equipment repair in Anaheim or a neighboring town.